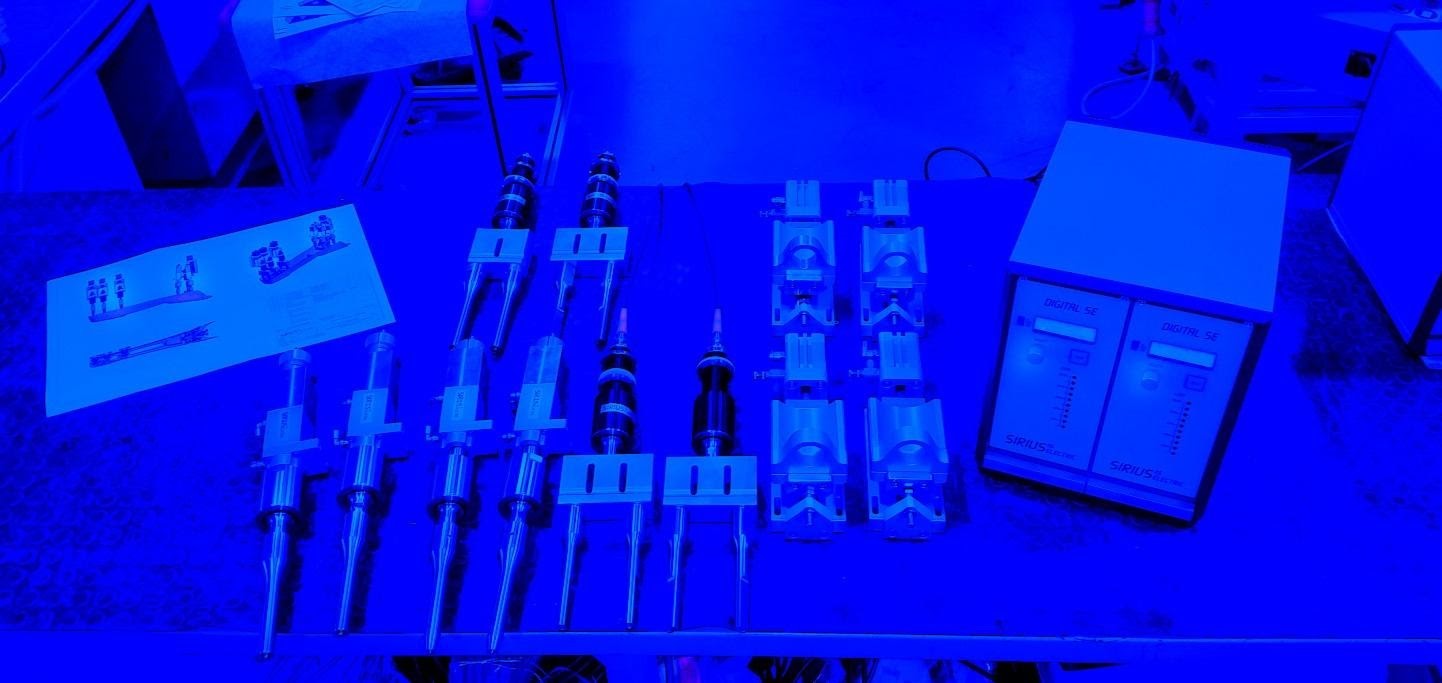
Quando parliamo di onde, occorre distinguere tra frequenze udibili e non udibili. La frequenza udibile delle onde meccaniche è compresa tra 16Hz e 16.000 Hz; quelle non udibili dall’orecchio umano al di sotto di 16 Hz sono chiamate “infrasuoni”, mentre quelle superiori ai 16.000 Hz, ULTRASUONI. In questo articolo, scopriamo insieme i principi di funzionamento di questa tecnologia e alcune linee guida di corretta saldatura.
Il principio di funzionamento della saldatura a ultrasuoni
Dal punto di vista fisico, la saldatura ad ultrasuoni è un fenomeno fisico e consiste nel moto alterno ripetuto attorno ad una posizione centrale o di equilibrio. Sollecita i particolari termoplastici, nella maggior parte dei casi ottenuti tramite stampaggio a iniezione e crea al loro interno una frizione intermolecolare progressiva che porta a un aumento localizzato di temperatura. Tale aumento, concentrato in un intervallo di tempo estremamente breve (nell’ordine dei decimi di secondo), provoca la fusione di un’area ben definita (l’area di giunzione) che, sotto l’azione di una forza costante, spinge due particolari a unirsi, penetrando uno nell’altro. I pezzi, quindi, si saldano senza il bisogno di colle o di additivi.
Come avviene il processo di saldatura?
Il processo di saldatura a ultrasuoni ha il suo cuore, vivo e pulsante, nel generatore. Formato da vari circuiti elettronici, il generatore di ultrasuoni ha il compito di trasformare l’energia di rete a bassa frequenza (50 Hz) e di elevarla a frequenza superiore (20 o più KHz) con una tensione ed una corrente proporzionale alla sua potenza. La potenza elettrica così generata viene trasportata da un cavo coassiale fino al convertitore (o emettitore), in cui ha origine la vera trasformazione elettro-meccanica delle vibrazioni. Le caratteristiche di questa vibrazione vengono trasmesse al particolare utilizzando una specifica frequenza (20, 30, 36, 40 kHz), un’ampiezza caratteristica (da 10 fino a 100 micron picco/picco), insieme a una forza e una durata, calibrate sulla base delle caratteristiche di conformità richieste. E’ comunque importante sottolineare che la potenza prodotta dal generatore a vuoto, cioè non durante una saldatura, deve essere più bassa possibile. Il convertitore (o emettitore) è un solido formato da elementi piezoelettrici e utilizzando il principio fisico della piezoelettricità , produce un’onda vibratoria stazionaria, che viene amplificata dai due elementi di trasmissione finale: l’amplificatore meccanico (o booster) e il sonotrodo.
Il pezzo da saldare, a contatto col sonotrodo, comincia a vibrare e a scaldarsi in maniera circoscritta nell’area di giunzione. Ha così inizio il processo di fusione. Il calore viene trasmesso per contatto al pezzo inferiore, che inizia il medesimo processo di fusione localizzato. Si può immaginare l’area di giunzione come la confluenza tra due fiumi che si mescolano insieme istante dopo istante. Lo stadio finale della saldatura prevede l’interruzione della vibrazione ultrasonica seguito da un tempo raffreddamento controllato in pressione (o in forza nei sistemi più evoluti), che porta alla risolidificazione e compattazione dell’intera area. Le strutture molecolari di due particolari distinti vengono così ricombinate insieme per la creazione di una zona comune di raccordo.
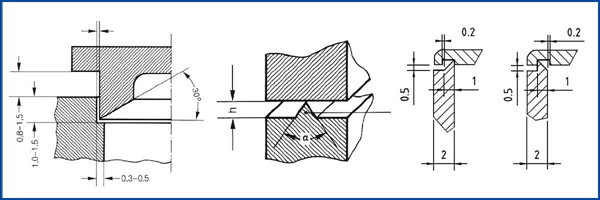
Quali materie plastiche saldare a ultrasuoni?
Le materie plastiche sono materiale ad elevata molecolarità (polimeri) oggi prodotte esclusivamente in modo sintetico. Si dividono in termoplastici; termoindurenti; elastomeri. I termoplastici sono materiali sensibili al calore che a loro volta si dividono in due grandi famiglie: i termoplastici amorfi e i termoplastici parzialmente cristallini o semicristallini. I materiali amorfi, hanno una struttura più rigida e definita, per questo sono anche i più adatti a essere saldati a ultrasuoni. La vibrazione ad alta frequenza viene generata dal convertitore e trasmessa al particolare tramite un utensile dedicato, chiamato sonotrodo. Le caratteristiche dei materiali amorfi offrono un mezzo materiale rigido che si adegua perfettamente alla trasmissione delle onde soniche.
I materiali semicristallini, sono invece adatti per una saldatura più prossima alla superficie di contatto del sonotrodo (denominato campo vicino e caratterizzato da una distanza tra sonotrodo stesso e area di giunzione, inferiore ai 6/8 mm).
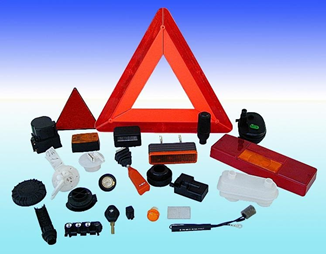
Vantaggi della saldatura a ultrasuoni
Tecnologia ripetibile ed estremamente rapida: pochi secondi per un ciclo completo, guarnizioni ermetiche eccellenti, garantite ad alte pressioni, non danneggia termicamente il materiale, costanza dei risultati per la resistenza alla torsione e alla trazione. Entrando nello specifico, il principale vantaggio è l’estrema direttività: solo la specifica area di giunzione viene coinvolta nel processo, e questo garantisce una fusione definita e precisa. Il materiale liquido viene convogliato, raccolto e successivamente compresso per formare un raccordo compatto e omogeneo. Attraverso uno specifico design del particolare, le onde ultrasoniche vengono convogliate e direzionate per limitare lo stress generale e ottimizzare la potenza utilizzata. Risultato: immediato utilizzo dei pezzi saldati.
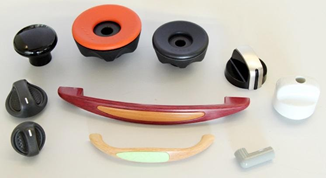
Linee guida generali per affrontare il processo
Una saldatura a ultrasuoni professionale si basa su tre fattori principali: uno studio approfondito delle peculiarità della singola soluzione, una valutazione prototipale che identifichi i parametri fondamentali di gestione e controllo (per esempio l’individuazione dell’ampiezza caratteristica, dell’energia richiesta e della quota di fusione) e un’implementazione produttiva guidata che punti a definire gli intervalli e i limiti di accettabilità del prodotto finale. Trascurare aspetti di carattere progettuale e scegliere una strumentazione non professionale porta spesso a commettere errori con un impatto non facilmente calcolabile.