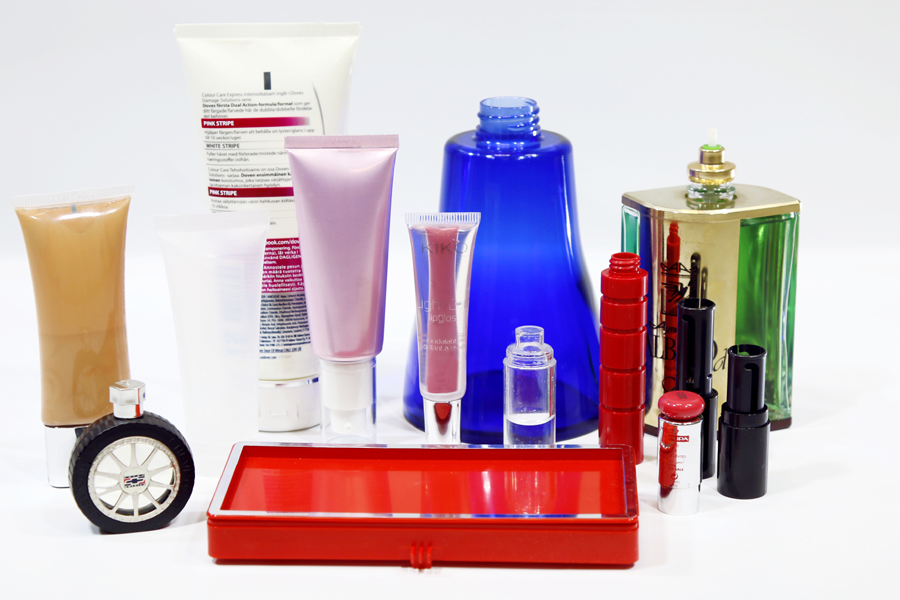
Among the methods to weld thermoplastic materials, ultrasonic and spin welding are among the most common technologies. In this article, we will explore together the difference between ultrasonic welding and spin welding, highlighting the fundamental characteristics for their fields of application.
Ultrasonic welding: a speed and precise technology for thermoplastics
From a physical point of view, ultrasonic welding is a mechanical vibration between 15 and 50 kHz with variable amplitude depending on the thermoplastic material to be assembled – generally between 20 and 100 microns peak/peak. This intense vibration is applied to the pieces to be welded, with a variable normal load. The parts to weld vibrate by means of the vibrating unit composed of the transducer and the booster, at the end of which the sonotrode is screwed. It stimulates the thermoplastic parts and creates an intense and progressive intermolecular friction inside them that leads to a localized increase in temperature. This increase in temperature causes the fusion of a well-defined area (welding joint) that, under the action of a constant force, pushes two details to join, penetrating one into the other. Ultrasonic welding allows a safe and durable joining of different products even with long life periods.
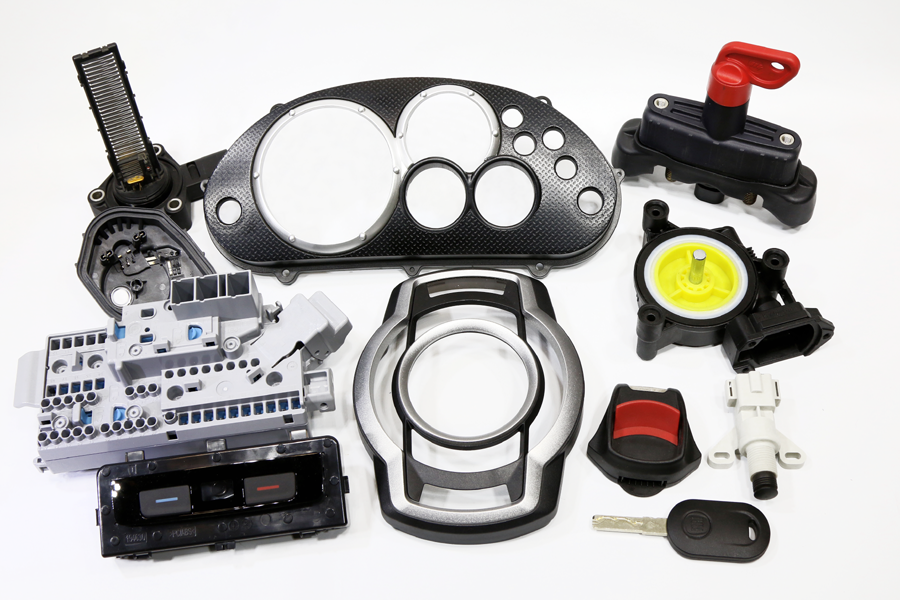
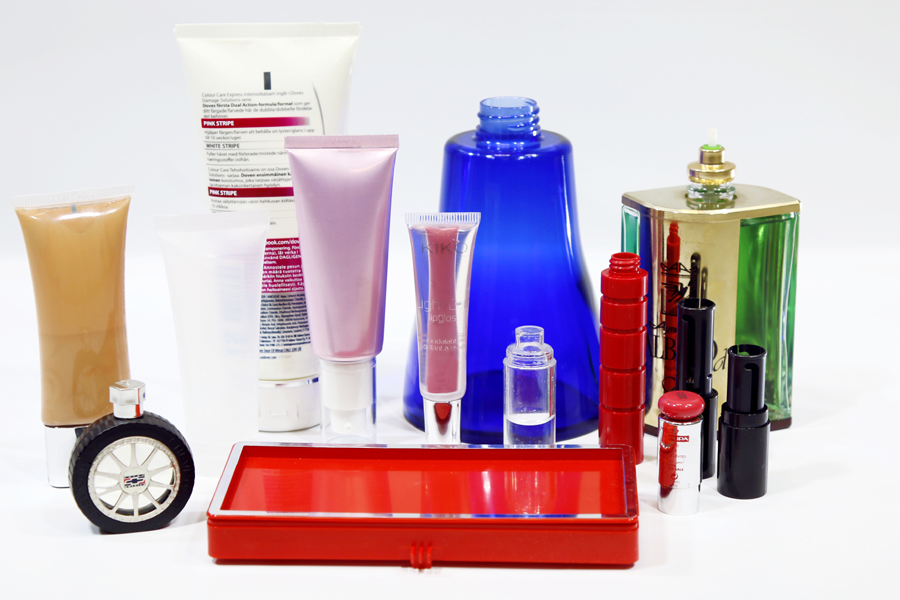
Spin welding: the best welding technology for circular pieces
As the name implies, in the spin welding the heat required for welding is produced by a rotary motion, combined with the thrust pressure. This process is only suitable for welding circular parts. If the components have different lengths, it is best to rotate the shortest to keep the masses in motion. The decisive factors for this technology are the geometry of the components, the expected production and the capital available. Since only a few mechanical components are needed, the equipment can also be built by the user himself. The spin welding is the ideal method to assemble pieces that have a circular shape or otherwise, that can freely rotate around their axis (e.g. water and air filters).
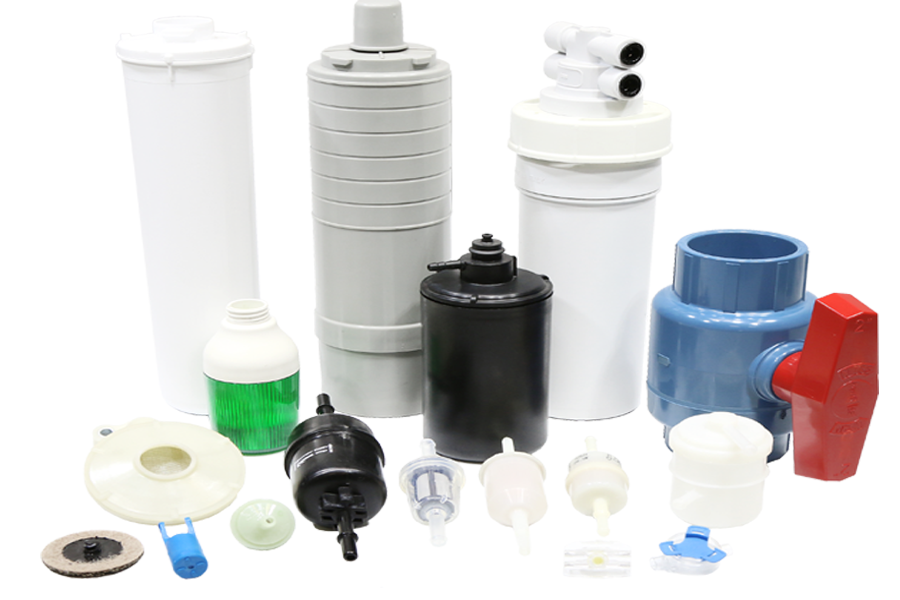
Technology comparisons: ultrasonic welding
Pros of ultrasonic welding:
– Repeatable and extremely fast technology. In some cases, a few tenths of a second
– Does not heat damage the material
– Excellent mechanical and aesthetic properties of welded parts
– Immediate use of welded parts possible
– Possibility of obtaining excellent hermetic seals
– Wide range of applications
– Possibility to automate the production process
– Excellent cost/application ratio
– Very low power consumption
Cons of ultrasonic welding:
– The material must be rigid to carry ultrasonic energy without having too much dissipation
– Difficulty in welding parts with complex geometries
– Difficulty of welding large pieces except with the use of special and expensive welding machines
– Possibility of damage to thin-walled workpieces
– Possibility of breaking parts with thin sections
– Careful study of welding joint